Rear and intermediate axles of motor grader DZ-98B
The motor grader is equipped with the interchangeable rear and intermediate axles.Each of the above-mentioned axles is essentially a steel beam in whose middle portion is fastened final drive bracket 23 with the mounted-on bevel gears with the circular tooth,while the final reduction gears are fastened to the flanges. Floating-type axle shafts 30 connect the final drive to the final reduction gears.The final reduction gear is a cylindrical gear with the internal meshing.
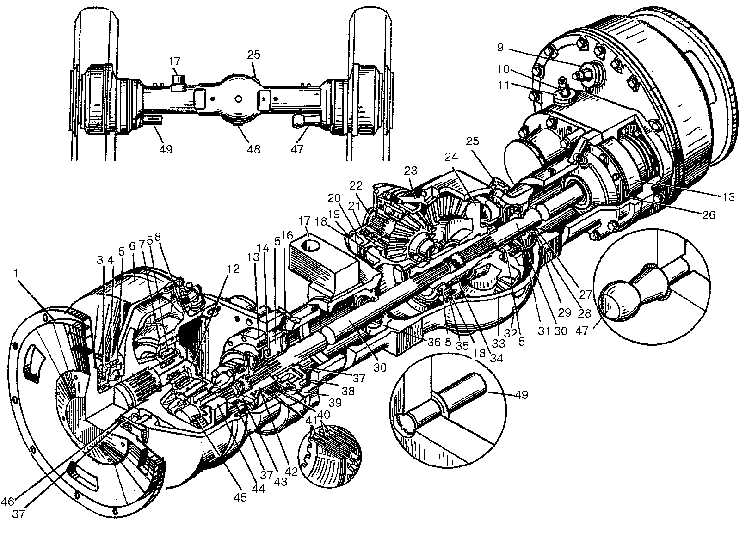
Small pinion shaft 45 of each final reduction gear is connected to the respective axle shaft by means of driving bushing 42 and flange 43. A multi-disc wheel brake with a pneumatic drive is mounted into each final reduction gear.
The brake discs are in the oil bath.
The brakes are fastened to two equalizers by means of ball pins 47 and cylindrical pins 49. Such kind of fastening ensures mounting of the axles.
Adjust meshing of the final drive bevel pair as follows: first set correctly gear 24 relative to bracket 23.The tooth point on the maximum diameter of the gear should be spaced at 25.7 mm relative to the edge of the fitting hole for the small gear sleeve. At the same time,a required clearance is ensured in conical bearings 5 (within 0.05-0.08 mm).Then measure the size in the assembled unit of small gear 22 from the tooth point along the greatest diameter up to the sleeve fitting plane. Deduct 40.3 mm from the said size and select adjusting gaskets 18 to suit the thickness which is equal to the obtained size.
Check the correct adjustment by the contact pattern (paint) or by the noise in operation. During normal operation of the gears the noise is low, monotonous, free of screeching sound or bumps. Check that the temperature of the unit during operation under load does not exceed 60 0C (check by touch, a hand should endure a long touch). Remember, that correct meshing of the bevel pair is obtained when the initial position of the gears is preserved. Therefore,during a forced disassembly of the final drive first of all remember disposition of the gears (the number of gaskets at each side) in order to ensure their correct reassembly. Do not readjust position of the gears (aimed at decreasing the backlash between the teeth which naturally increases as the gears become worn out).
Proceed with the above-mentioned adjustment only in case of mounting of new pair of the devel gears.
Wear-rejection size of the gears is the backlash of 2.5 mm during the correct meshing. Change the gears in all the axles only in pairs.